Präzise kommunizieren und planen, bevor es brennt
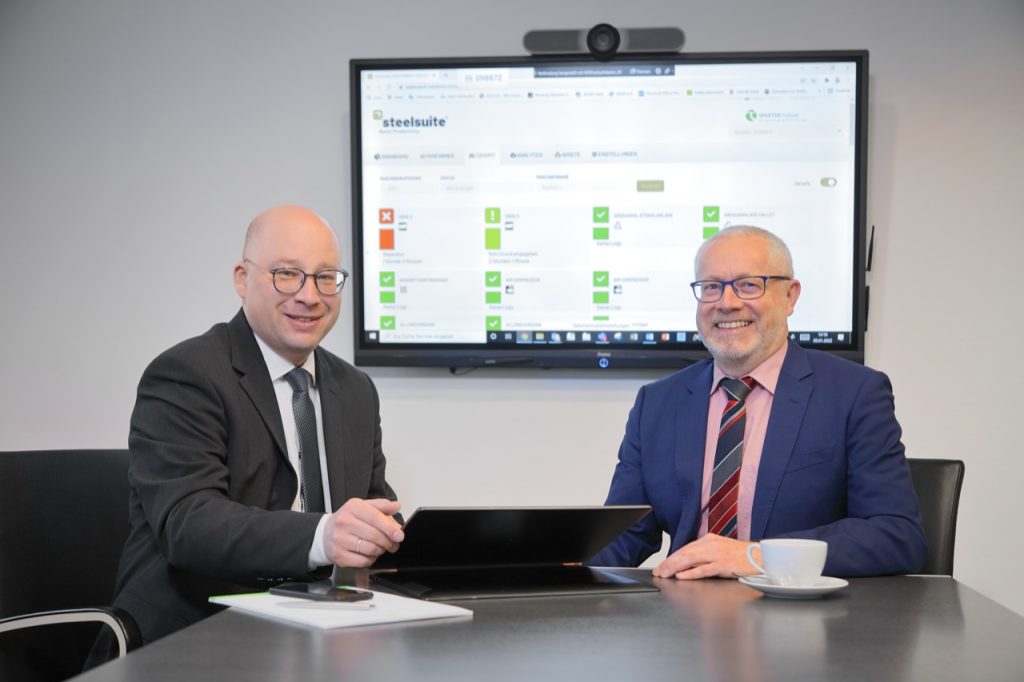
Die Carl Spaeter-Gruppe entschied sich nach guten Erfahrungen aus zwei Pilotprojekten im Herbst 2021 dafür, die Lösung der Kaltenbach.Solutions GmbH für die Betriebsmittelverwaltung innerhalb von nur 15 Wochen an allen 19 Betriebsstandorten in Deutschland einzuführen, um künftig sämtliche Arbeitsabläufe und die Dokumentation rund um alle Betriebsmittel vollständig digital abzubilden.
Das Ziel: Alle Standorte, Maschinen, Anlagen und Geräte einheitlich im Überblick
„Die durchgängige Digitalisierung betrieblicher Abläufe ist für uns als Stahlhändler essentiell, um vor dem Hintergrund des demographischen Wandels auch künftig unsere Kundschaft bei steigenden Anforderungen an Termintreue und Qualität verlässlich zu versorgen. Nur so werden wir unserer Funktion als Problemlöser in einer globalisierten Supply Chain gerecht.“
(Klaus Tissen, CFO der Carl Spaeter-Gruppe)
Mit einer Tradition von mehr als 140 Jahren agiert die Carl Spaeter-Gruppe heute als größter werksungebundener Stahlhändler Deutschlands. Vom Hauptsitz in Duisburg und den Standorten im gesamten Bundesgebiet aus vertreibt die Gruppe insbesondere Walzstahlprodukte jeglicher Art, Edelstahl und Aluminium-Halbzeuge und gehört gemessen am Umsatz zu den 500 größten Unternehmen Deutschlands. In Umsetzung der Digitalisierungsstrategie der Gruppe wurde im vierten Quartal 2021 die Entscheidung getroffen, eine einheitliche und vollständig digitale Betriebsmittelverwaltung einzuführen.
Um dieses Vorhaben zuverlässig umzusetzen, wurden die Experten der Kaltenbach.Solutions GmbH beauftragt. Einbezogen wurden insgesamt 15 Organisationseinheiten mit 19 Standorten in ganz Deutschland. Zu den vorhandenen Betriebsmitteln gehören rund 150 Maschinen in der Anarbeitung, über 200 Krananlagen und mehr als 1.000 weitere Geräte und Fahrzeuge. Neben der digitalen Unterstützung aller rechtlichen Dokumentationsanforderungen den Maschinen- und Anlagenpark betreffend, der Optimierung der Abläufe in der Wartung und Instandhaltung sowie konsequenter Erfüllung höchster Standards der Arbeitssicherheit, soll mit dem Projekt eine Steigerung der Verfügbarkeit der Maschinen in der Anarbeitung um mindestens 10% erreicht werden. Diese Verbesserung bildet die Grundlage dafür, mit dem Wachstum des Unternehmens die Lieferversprechen gegenüber den Kunden verlässlich und nachhaltig einhalten zu können.
Das Vorgehen: Erstellen eines detaillierten Stufenplans für die schrittweise Umsetzung
Unter der Projektleitung von Thomas Schröder (Betriebsleiter der F. Hackländer GmbH, Kassel) wurde zunächst ein detaillierter Stufenplan und die verbindliche Festlegung von Verantwortlichkeiten ausgearbeitet. Die Planung und Umsetzung des Projektes wurde durch einen Lenkungsausschuss in Verantwortung von Klaus Tissen (CFO der Carl Spaeter-Gruppe) begleitet.
Die Herausforderung bestand darin, in nur wenigen Wochen rund 1.400 Betriebsmittel zu erfassen und digital abzubilden. Gleichzeitig sollten bisher uneinheitliche Abläufe und Vorgehensweisen in der Verwaltung sowie bei der Pflege, Wartung und Prüfung von Betriebsmitteln gruppenweit vereinheitlicht werden. Auch der Umgang mit Störungen und Stillständen von Maschinen sollte standardisiert werden.
Ein zentraler Punkt des Vorhabens war die Frage, auf welche Art und Weise die mehr als 700 User an das neue System schrittweise herangeführt werden können. Vor Beginn der Umsetzungsphase war zunächst eine genaue Ist-Aufnahme notwendig. Im ersten Schritt wurden daher sämtliche Betriebsmittel sowie alle User nach definierten Standards mittels Excel-Templates erfasst.
Im Anschluss fand eine umfassende Überprüfung der festgehaltenen Daten mit Hilfe automatischer Prüfroutinen statt, um vor dem eigentlichen Digitalisieren der Betriebsmittel mögliche Daten-Inkonsistenzen zu beseitigen. Im dritten Schritt erfolgte dann das Abbilden der Betriebsmittel auf der Branchenplattform steelsuite der Kaltenbach.Solutions. Auch hier kamen Routinen für die Massenverarbeitung von Daten zum Einsatz, um das Fehlerrisiko auf ein Minimum zu reduzieren. Wie bei allen Digitalprojekten ist die Qualität der Stammdaten einer der erfolgsrelevanten Faktoren. Im letzten Schritt wurden die Betriebsmittel mit den vordefinierten Pflege- und Wartungspläne verknüpft und das System in Betrieb genommen.
Die Schulung der User erfolgte durchgehend nach dem Train the Trainer-Konzept. Dafür standen an jedem Standort ein bis zwei Mitarbeiter zur Weitervermittlung der Vorgehensweise an die User zur Verfügung. Die Schulungen selbst fanden Pandemie-konform online über Microsoft Teams statt. Für die tägliche Arbeit bekamen alle Nutzer einen übersichtlichen Leitfaden. Gruppe für Gruppe konnten die Teams dann live gehen. Für Rückfragen stand der Customer-Support der Kaltenbach.Solutions zur Verfügung.
Das Maschinen-Monitoring: Zentrale Module und ihre Verwendung an den Standorten
Wo früher die Betriebs- und Schichtleitung alle Informationen zum aktuellen Zustand der Maschinen und Anlagen einzeln einsammeln musste, reicht heute ein Blick auf das sogenannte Cockpit. Es zeigt aktuelle Maschinen-Zustände in einfachen Grafiken an und macht Probleme schnell sichtbar. Über die Menüpunkte „Wartung“ und „Pflege“ lassen sich die Abläufe im Zusammenhang mit der Wartung, Pflege sowie UVV-Prüfungen von Anlagen, Maschinen und Einzelgeräten steuern. Die Software stellt dafür relevante Daten als einfache Grafiken dar. Damit wird sofort erkannt, ob und an welchen Betriebsmitteln Probleme vorliegen. Die Ansicht „Stillstand & Störung“ zeigt die passenden Prozess-Lösungen zur Behebung an. Das digitale „Logbuch“ erfasst alle Ereignisse und schafft Transparenz. So haben die Nutzer jederzeit einen Überblick über die bisherigen Aktivitäten. Im Punkt „Asset Management“ ist es zudem möglich, die Verwaltung von Maschinen, Anlagen und Geräten sinnvoll zu strukturieren.
Klickt der User auf den Menüpunkt „Gut zu Wissen“, findet er arbeitsplatzbezogene Informationen in übersichtlich aufbereiteter Form – eine Art Wissens-Datenbank, die regelmäßig aktualisiert wird. Hierzu gehören zum Beispiel alle QM-relevanten Arbeits- und Sicherheitsanweisungen. Technische Informationen zu den Betriebsmitteln werden unter dem Stichwort „Dokumente“ in digitaler Form bereitgestellt. Hier haben die Nutzer Zugriff auf Betriebsanleitungen, Ersatz- und Verschleißteil-Listen, Rechnungen und andere Dokumente. Der Unterpunkt „Support“ dient der Kommunikation zwischen dem Shopfloor und den Mitarbeitern im Büro. Wenn es brennt, kann hier ein beschleunigter und lösungsorientierter Informationsaustausch stattfinden. Im „Chat“ läuft der maschinenbezogene Austausch in Form von Chatgruppen.
Der Zeitrahmen und das Ergebnis der Carl Spaeter-Gruppe
Die Vorbereitungsphase des umfangreichen Projektes begann Anfang September und dauerte vier Wochen. Von Oktober bis Ende Dezember nahm die Umsetzungsphase anschließend rund zwölf Wochen in Anspruch. In den Dezemberwochen erfolgte sukzessive der Live-Gang aller beteiligten Niederlassungen und der erfolgreiche Projektabschluss. Damit lag die Gesamtdauer des Projektes bei insgesamt fünfzehn Wochen.
„Mit der steelsuite-Betriebsmittelverwaltung haben wir nunmehr den Betriebsstatus unseres Anlagen- und Fuhrparks jederzeit – auch mobil – im Überblick und Zugriff. In der Summe wird die Zuverlässigkeit und Verfügbarkeit sämtlicher Aggregate spürbar verbessert.“
(Klaus Tissen, CFO der Carl Spaeter-Gruppe)
Im Bild von links nach rechts zu sehen: Klaus Tissen und Valentin Kaltenbach.
Die Reportage ist in Heft 1/22 des Fachmagazins “Stahlreport” erschienen.